CKC has continuously improved technology
and widened range of products to serve customers. Moreover, CKC has delivered
various type of Automatic Filtration System, Pressure Vessel, SCR (Selective
Catalytic Reduction) System, Auto Strainer, Metallic Filter Cartridge and Gas
Dehydration System.
 
|
 |
In every process involving contact between liquid and
flowing gas, tiny mist droplets are carried away with the gas. This phenomenon
is called entrainment.
Beginning about 1947, special devices were
developed to remove mist from gas streams. Now known as mist eliminators, these
devices provide a large surface area in a small volume to collect liquid without
substantially impeding gas flow. Unlike filters, which hold particles
indefinitely, mist eliminators coalesce (merge) fine droplets and allow the
liquid to drain away. Gas typically flos upward through a horizontal mist
eliminator.
More recently, advances in technology have enabled
substantial progress in mist eliminator designs, materials, and application
expertise. New products and methods of use have been found highly effective for
many purposes, especially the following:
? Increasing throughput ?
Downsizing new vessels ? Improving product purity ? Cutting operating
costs ? Reducing environmental pollution ? Reducing downstream
corrossion ? Increasing recovery of valuable liquids
In today?s era of
higher expectations of mist eliminators, achieving such benefits requires better
knowledge on the part of users. It is no longer adequate for a designer simply
to indicate ?mist eliminator? in a drawing. The results will depend on proper
specification of mist eliminator type (or combination of types), orientation,
thickness, internal details, support and spacing in the vessel, vapor velocity
and flow pattern, and many other considerations.
Despite the advances
that have been made, mist eliminator specification is still as much art as
science. For all but the most experienced users, proper application depends on
consultation with a manufacturer?s engineers. Such help should be considered for
every new mist eliminator application as well as every upgrade or
debottlenecking of existing applications.
TO MAKE THE MOST of a mist
eliminator investment, the designer should become familiar with the
considerations and possibilities involved. Due to the numerous variables
involved in specifying mist eliminators, designers and purchasers should consult
with Amistco?s separation specialists before making a final decision. |
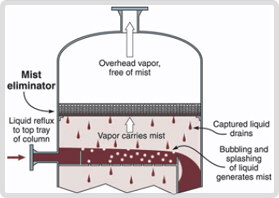 |
Mechanical |
Column packing or trays |
5 to 800 μm |
Sprays |
10 to 1,000 μm |
Surface evaporation |
3 to 1,000 μm |
Chemical |
Acid mists |
0.1 to 15 μm |
Condensation |
Blown off heat exchanger surface |
3 to 500 μm |
In saturated vapor |
0.1 to 50
μm | | | |